Laser Processing: Solution for Vascular Devices
Medical devices are becoming more complex, requiring tighter manufacturing processes for stability and performance.
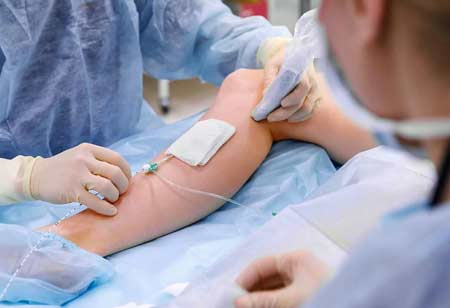
By
Medical Care Review | Thursday, May 16, 2024
Stay on top of your health and well-being with exclusive feature stories on the top medical clinics and treatment centers, expert insights and the latest news delivered straight to your inbox. Subscribe today.
Laser processing, introduced in the 1990s, has advanced medical technology, providing quality and broad access to vascular interventional devices for combating conditions like strokes and heart valve failure. Laser technology has become the standard for producing intricate devices for several reasons.
UNMATCHED PRECISION WHEN CUTTING OR JOINING
Medical devices are becoming more complex, requiring tighter manufacturing processes for stability and performance. Lasers offer close control over material processing, delivering singledigit micron kerf with accurate spot size placement. They can remove atoms or cut through entire thicknesses with zero contact and wear, creating innovative products with more minor features and more precise manufacturing processes.
ENHANCED PROCESS CONTROL AND REPRODUCIBILITY
Lasers offer high production control for medical device manufacturers when integrated with automated machines. These stable systems enable historical analysis of quality metrics and can be calibrated with advanced sensors to minimize variation to near zero, ensuring consistent quality across manufacturing lots.
MINIMIZED HEAT-AFFECT ZONES (HAZ)
Medical devices rely on thermally sensitive materials like nitinol, which can be affected by excessive heat. Advances in laserand automation technologies enable controlled beam pulses in the femtosecond time domain, allowing for minimal HAZ processing of these materials using ablative techniques.
IMPROVED THROUGHPUT
Laser processing offers improved speed compared to traditional mechanical machining processes. Traditional machine techniques often negatively affect throughput. Advanced motion control systems with short-pulse lasers and tightly coupled machine controls can deliver laser energy to parts at desired positions, optimizing motion paths for higher speeds and accelerations, resulting in a significant throughput advantage.
MINIMIZED POST-PROCESSING
Laser processing offers a cleaner alternative to traditional machining due to reduced debris generation and more straightforward material clearance. Chemical post-processing removes tiny amounts of dross, while ultra-fast lasers for laser ablation virtually eliminate HAZ and dross. Laser machining doesn’t require chemicals, flux, or pigments.
WHAT’S THE CATCH WITH LASER PROCESSING?
Laser processing is the primary method for machined vascular devices, but manufacturers often face short payback periods due to cost savings in quality and throughput. To maximize the benefits of laser processing, manufacturers must engage with machine OEMs and push for more than just a “black box” to fully utilize its capabilities.